In fin tube heat exchangers, the fluid (gas/water/glycol/refrigerant/etc.) circulating through the coil’s tubes is extremely important for the coil’s overall performance – it’s half the battle, along with airside heat transfer. The degree to which the fluid contacts the tube walls affects the coil’s performance and influences a system's overall efficiency – the more the fluid comes into contact with the tube wall, the better – and more economical – the heat transfer.
One method used by coil manufacturers to increase the efficiency of heat transfer equipment – particularly in applications involving fluids with low velocity, high-viscosity, or both – is by creating turbulence within the heat exchanger’s tubes. By doing so, turbulent flow is achieved, which, relative to the less energetic laminar flow, makes for increased contact with tube walls.
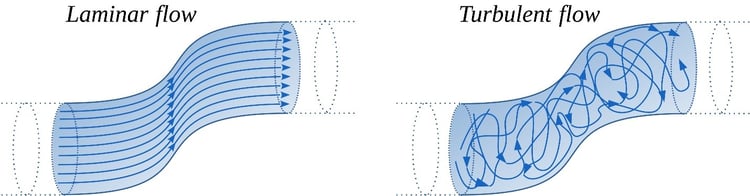
One means of achieving this desirable turbulent flow is through devices called turbulators, which alter fluid’s flow, maximizing contact with the tube wall. Turbulators also reduce the boundary layer in a tube – which is the small area near the tube wall, where the effects of viscosity are amplified, and heat transfer tends to be relatively poor. At SRC, questions from customers about turbulators are common. What is a turbulator? What are the different kinds of turbulators? Are turbulators worth it? This blog aims to answers those questions.
Work in HVAC? Check out SRC's Refrigerant Guide and never Google refrigerant properties again. It's brand new and completely free!
A primary benefit of the turbulators is a smaller footprint for the coil. Depending on the application, adding turbulators to a coil can result in a significant reduction in coil size without compromising on thermal performance.
For instance, in an example system, a 45” x 45” coil operating with a working fluid consisting of 35% glycol, the addition of turbulators can reduce the number of tube rows required by as much as half.
There are four common types of turbulators seen in heat exchangers: ball, twisted tape, spring, and matrix.
- Ball Turbulator
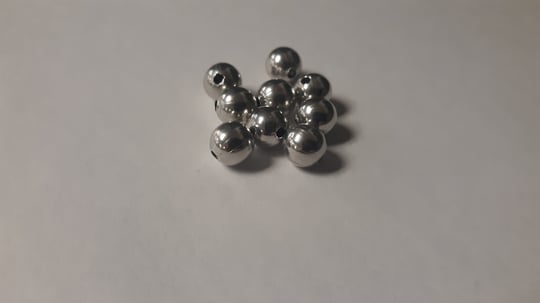
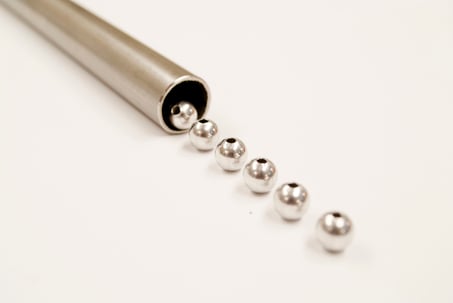
Ball turbulators are true to their name – small balls, usually made from aluminum, used to affect the flow of the working fluid in a given coil. They do so by taking up space within the tube, increasing velocity by reducing volume.
Of the turbulators covered in this post, ball turbulators are the most effective, as they best reduce the internal surface area of the tube. However, with that reduced surface area comes the highest pressure drop of the four turbulators discussed in this piece. Like several other elements of heat transfer, the expression “if some is good, more is better” does not apply, as an optimal balance between pressure drop and ideal turbulence must be attained.
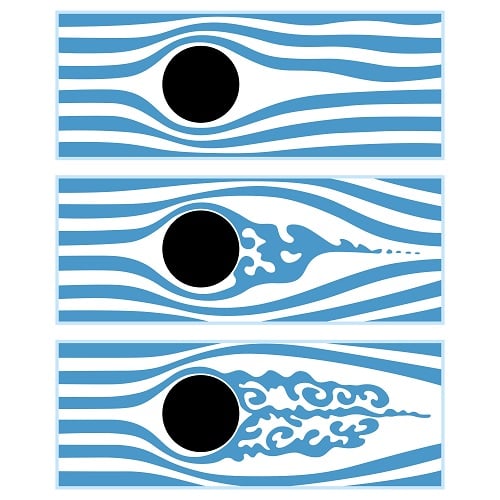
With regard to cost, ball turbulators are fairly inexpensive, but should be purchased to stock if used regularly to best realize the value.
- Spring turbulator

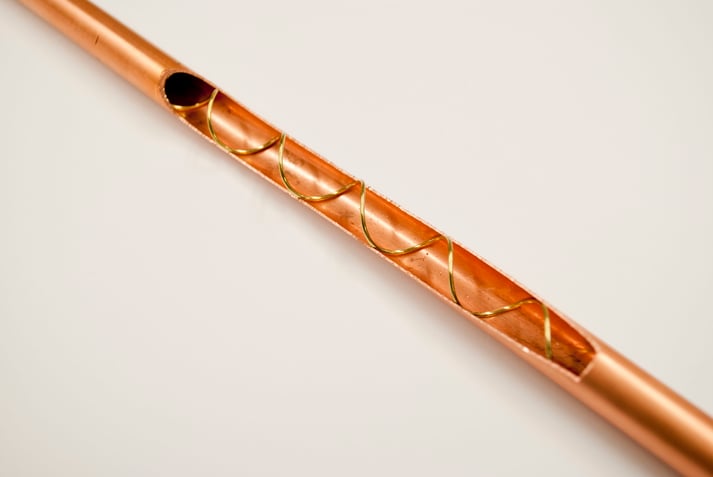
Another example of the excellent naming abilities of its creators is the spring turbulator, which is a coiled spring. They’re sold as tightly wound coils (picture a small-diameter slinky) and then stretched out inside the tube (picture a ruined small-diameter slinky). Small hooks at either end of the tube, combined with a snug fit within the tube’s internal diameter prevent the spring from returning to its original shape and establish contact between the spring and tube wall.
Spring turbulators create a wave-like motion, directing fluid energy up and down more so than imparting spin. This motion channels the fluid toward the tube walls, eating into the boundary layer and improving heat transfer.
They can be made from a number of materials, but ours are typically made from brass, and they offer an excellent balance of relatively low cost and good performance. Like ball turbulators, springs’ value is best realized when ordered in bulk and stocked for specific diameter tubes.
- Twisted tape turbulator
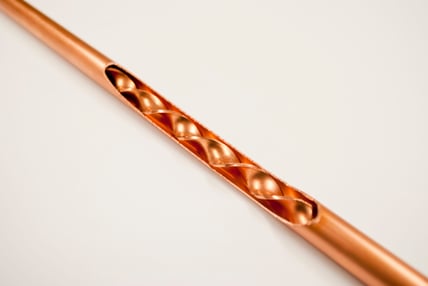

These helically shaped rods are inserted into heat exchanger tubes, where they create turbulence. They create turbulent flow in a method similar to that of a spring turbulator, but not identical, and can be made from any number of materials.
Twisted tape turbulators essentially bisect the tube’s internal diameter, coming into contact with the tube wall, where they create turbulence and channel the flow away from the tube’s center outward to the boundary layer. This makes the fluid nearer the wall more turbulent than in the center, which is desirable, as the bulk of the heat transfer occurs in this region of the tube.
Twisted tape turbulators’ performance is marginally better than spring turbulators, but the price is much greater, and costs add up quickly depending on number of tubes. Lead time for twisted tape turbulators is longer as well, as each turbulator must be made according to the tubes’ specific lengths. The customer can also specify the number of twists per foot, depending on the required level of turbulence.
- Matrix turbulator
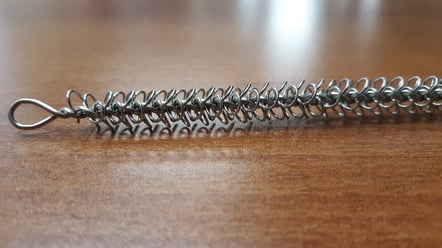
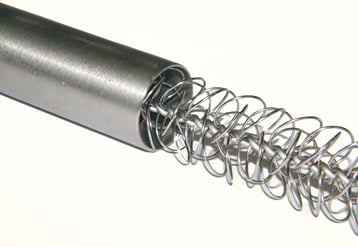
photo credit: CALGAVIN's hiTRAN® Thermal Systems
The matrix turbulator consists of a twisted wire rod adorned with thin wire loops along its length. Typically made from stainless steel, these devices serve as static mixers, churning the fluid and imparting turbulence. Like twisted tape, these must be made custom for each coil, resulting in higher cost. Contributing to that higher cost and - high performance - is the fact that the configuration and density of the matrices can be changed to meet the needs of a given application.
Lead times for these turbulators can be longer, too, sometimes 10 weeks or more depending on the supplier’s location. Their cost can be prohibitive, and while they’re not the right choice for several jobs, but they’re very effective in applications where it makes sense to use them. Matrix turbulators make economic sense for large coils, like those seen in air coolers for example. Moreover, the precision of their design allow engineers to very accurately calculate things like performance and pressure drop.
Don’t get left out in the cold when it comes to heat transfer information. To stay up to date on a variety of topics on the subject, subscribe to The Super Blog, our technical blog, Doctor's Orders, and follow us on LinkedIn, Twitter, and YouTube.