At Super Radiator Coils, our mission is unleashing the power of thermodynamics to improve our world, and when it comes to the industries and applications we support, few fit that mission better than pollution control. Heat transfer is used for a litany of pollution control functions – from condensing harmful vapors out of exhaust streams to reducing or repurposing thermal energy from industrial process emissions to lessen its impact on the environment.
The Application
We were recently consulted on a pollution control application that was new to us and that we found interesting. An engineer approached us looking for help designing a chilled water coil which would be used to condense vapor – specifically a C10/C11 alkene solvent – from an exhaust stream to reduce emissions at an industrial manufacturing facility.
One aspect that made the application challenging was the fact that multiple vapors – water vapor and the alkene solvent – needed to be condensed from the airstream, each with their own unique properties. The humid environment in this application affected the dew point temperature of the exhaust gas – a critical value for condensing applications – adding complexity to the necessary engineering calculations.
Another interesting wrinkle to the application was that this project was a retroactive measure to comply with emissions regulation. Original plant designs specified a different process for managing these VOC emissions but was not included during construction due to an oversight. This led the plant's operators to pursue a vapor recovery heat transfer solution that could be added without overhauling the plant’s schematic. This order of operations is somewhat atypical in our experience, but it was interesting to learn that a retroactive addition is possible.
Our Approach
After determining we’d be able to meet the requirements of the application, we then factored in plant-specific dynamics to maximize the utility of the equipment to overall facility operations. We proposed a 40” x 40” 12-row heat exchanger featuring 304 stainless tubes and corrugated aluminum fins to meet the requirement, which was compatible with the plant’s existing space. Some additional considerations we made were:
- The heat exchanger was designed to operate using existing plant utilities to minimize impact on the manufacturing process and plant design. We opted for a 12-row design to maximize heat transfer and get as close as possible to the available water temperature on the leaving air side.
- We also recommended a removable housing with an empty slot to accommodate an additional heat exchanger if the application required it in the future. This slot can also serve as an access area for cleaning in place procedures until a second heat exchanger is added. We also included drain pans for condensate capture, which were designed to be sufficient in the event a second coil was added. Below is an example of a slide-out housing design we built for a different application.
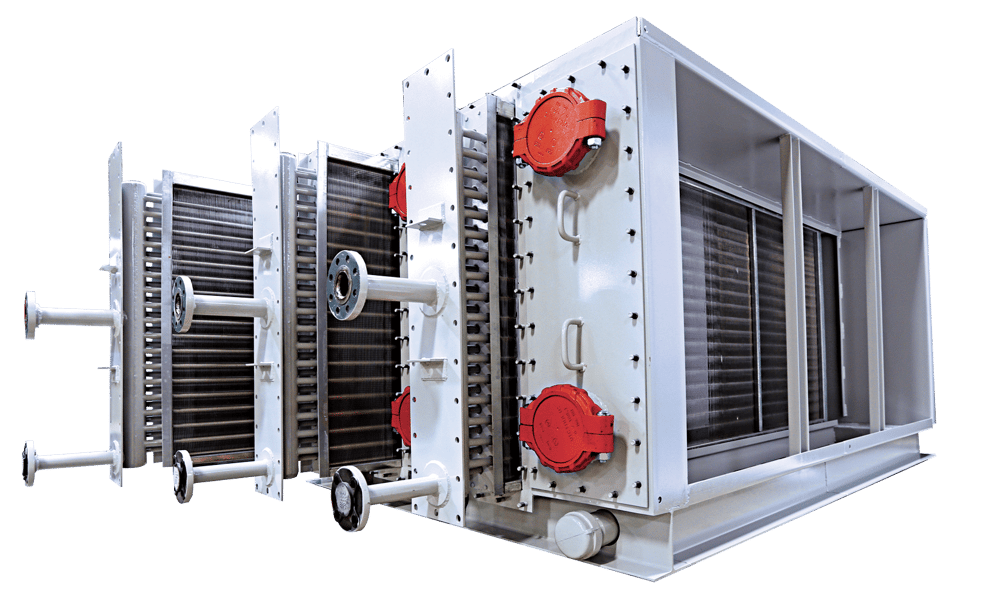
- Our proposed design also includes provisions inside the housing structure to support carbon filters downstream of the heat exchanger to capture any residual fine particulate.
Summary
Of the applications that we support regularly, pollution abatement and solvent recovery are two that we feel have among the most direct impact on the world around us and are excellent examples of the importance of engineering and heat transfer. Applications like these are also rewarding challenges for our engineers and serve as great opportunities for them to put their heads together with customers’ engineering teams to design a piece of equipment that does exactly what the application calls for.
If you’re a plant operator looking for help with emission reduction or you're just curious about some ways that heat transfer can improve your plant’s operational efficiency or effectiveness, touch base with our engineering team. We have several engineers who specialize in these sorts of applications who would love to hear more about what you’re working on.
Don’t get left out in the cold when it comes to heat transfer information. To stay up to date on a variety of topics on the subject, subscribe to The Super Blog, our technical blog, Doctor's Orders, and follow us on LinkedIn, Twitter, and YouTube.