There are terrific braze joints, awful braze joints, and everything in between. Today, we’ll examine one type of defect that can have devastating effects on joint integrity – flux entrapment.
What is flux?
To fully understand what flux entrapment is, we first need to talk about flux. Flux is a substance (combination of borates, fused borax, fluoborates, boron, chlorides, acids, to name a few) used in the brazing process to protect the metals from oxidation, among other functions. It also eliminates any oxides that form as the metals are heated or that may have been missed when the metals were cleaned prior to brazing. Flux also eases the flow of the filler metal by reducing surface tension.
Flux has multiple functions and takes on multiple forms during its performance of those functions. These forms occur at different stages of the brazing process as temperatures increase. In the first stage, which occurs at 212 degrees Fahrenheit, the water portion of the flux boils off.
Next, at around 600 degrees Fahrenheit, the flux turns white and bubbles form evenly across the surface, indicating a uniform transfer of heat. At 800 degrees Fahrenheit, the flux turns opaque and spreads out across the base metal, acting as a protective layer against oxygen. At 1100 degrees Fahrenheit, the flux becomes clear and liquid. At this stage, the chemicals in the flux are active and working to rid the surfaces of any remaining oxides and establishing a clean surface for bonding.
What is flux entrapment?
As its name implies, flux entrapment involves the encasement of surplus flux in a braze joint. There are a few potential culprits when flux entrapment occurs.
At Super Radiator, one way we apply flux to joints is with a brush. As the part heats up, the flux is activated, consuming oxides on the surface of the parts about to brazed. It’s around this time that the braze material should be added to the equation.
Ideally, the flux on the surface of the part is supplanted by the incoming braze material, pushing surface flux out of the joint. When this doesn’t occur properly, the exiting flux doesn’t get out of the way of the braze material, rather it’s consumed, trapping the flux in a bubble of braze material. This is a flux entrapment – flux is trapped in the braze joint, resulting in a weak joint and possible leaks in the field. Below is an example of an instance of flux entrapment at a coil's return bend.
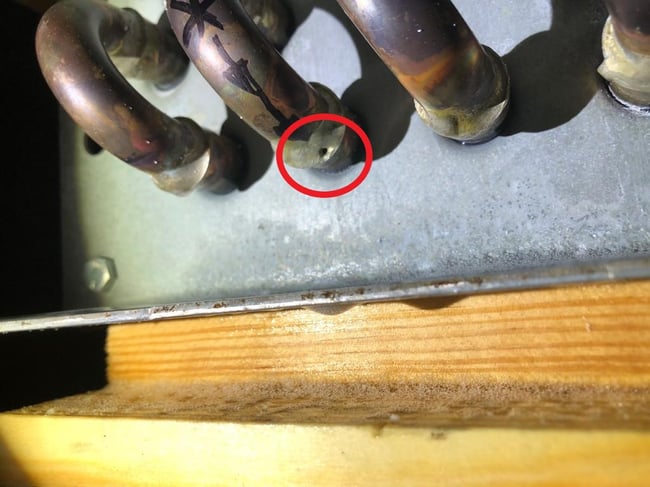
There a few different ways that flux entrapment occurs, but it tends to be a symptom of braze joints where proper clearances are not held. This issue can be created in the design process – i.e. the joint’s design didn’t include the necessary space required for the flux to fully do its job. Below is a cross section of a joint revealing an instance of flux entrapment.
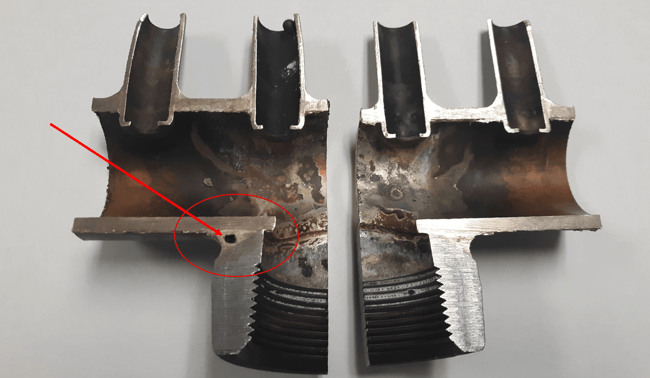
Flux entrapment can also be the result of a fit-up issue by the braze operator. For example, flux entrapment issues tend to arise more frequently when joining materials of different thicknesses – more flux is needed, the materials heat up at different rates making it harder to achieve the proper balance, making for a more challenging joint overall.
Don’t get left out in the cold when it comes to heat transfer information. To stay up to date on a variety of topics on the subject, subscribe to The Super Blog, our technical blog, Doctor's Orders, and follow us on LinkedIn, Twitter, and YouTube.